Guide to Selecting and Sizing
Industrial Caliper Brakes
Need help picking the right industrial brake for your application? You’re in the right place. This page covers some of the different kinds of caliper disc brakes available, their pros and cons, and how to select the right one for what you need to do. This video can help you get started.
Menu
Don’t have time to read it now?
Email it to yourself.
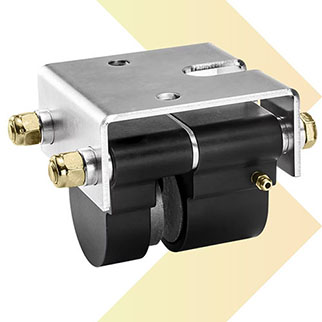
What Kind of Industrial Brake Do You Need?
Caliper disc brakes can slow, hold, and stop very heavy and/or fast-moving objects quickly. They are great when high torque, high energy stopping, and/or tensioning is required.
There are brakes that are pneumatic (powered by compressed air) and hydraulic (powered by compressed fluid). Other brakes incorporate a spring into their design. These spring applied brakes can be powered either by pneumatics or hydraulics. There are also mechanical brakes that operate with a simple lever and require no external power. The pros and cons of each type of industrial brake are explained in greater detail below.
Selecting the Right Industrial Caliper Brake Type
In order to pick the right kind of industrial brake, begin by thinking about how and where it will be used. Here are some of the questions you should consider.
- What is the power source available in your facility? Do you have existing shop air that makes pneumatic brakes easy to add? Do you already have hydraulic lines that can be used?
- Will the brake be inside or outside?
- What will the ambient temperature range be?
- Is the application static or dynamic? This is common in industrial applications where parts are rotating. Think of a winch that must be held in place after its reeling is complete.
- Is it an emergency brake that will only deploy once in a great while? Is it for a tensioning application like winding or unwinding something with torque levels constantly changing?
- Will the brake be working in a linear motion (like on a rail) or on a rotor going against a disc that is spinning?
- Do the pads need to be retracted off the braking surface when not in use?
- How much space do you have to add this brake?
- Is there a maximum allowable disc diameter and thickness that will work?
- Are there any mounting limitations?
Disc Brake Caliper Types Explained
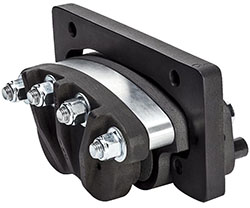
Pneumatic Brakes
A pneumatic brake requires compressed air to operate - usually supplied by a pneumatic pump. These brakes typically operate with air that is at 70 to 120 psi and max out at 200 psi. Many manufacturing facilities and factories already have a pneumatic compressor on site, so air brakes often make sense in these facilities. If compressed air is already available, pneumatic brakes are typically less expensive than adding hydraulic or electrical systems.
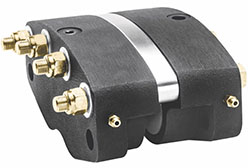
Hydraulic Brakes
A hydraulic brake is powered by compressed fluid. Fluids can be used at higher pressures than air, which makes hydraulic brakes ideal when you need to stop, hold, or tension equipment with higher torque. The most common fluids used are hydraulic oil or DOT 3/4 automotive brake fluid (polyethylene glycol). It’s important to select the correct model with seals that correspond with the type of fluid you’re using in your hydraulic brakes.
Hydraulic brakes are used in industrial equipment where a high braking force is required. These include many mining, oil field, agricultural, or similar heavy duty equipment applications. They are also common in vehicles, such as commercial and off-road type braking.
If a manufacturer already has shop air but needs the higher braking force of hydraulics, you can purchase air/oil intensifiers to convert shop air to hydraulic pressure. This is a cost-friendly solution for increasing braking force.
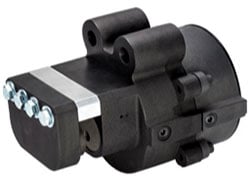
Spring Applied Brakes
Standard hydraulic and pneumatic brakes apply pressure to activate the brake piston(s). When pressure releases, the brake releases. Spring applied brakes work differently. Internal springs apply the force, but it is disengaged as long as there is power being fed into it (that can come from a hydraulic or pneumatic system). When the power is off (like if there is a loss of hydraulic or pneumatic pressure), the springs engage and braking force is applied.
Spring applied brakes are best for emergency stop applications and are often referred to as “fail-safe”or “E-stop” brakes. They offer redundancy and an extra level of safety in applications that involve suspended loads or potential motion.
They also work well for static holding applications, where a load must be held while another operation takes place. Other applications for spring applied brakes include robotics, rotary indexing equipment, and elevator e-brakes.
Many pneumatic spring applied brakes can operate on standard shop air because it takes only 85 psi of active air pressure to release the brake piston and store the energy in the Belleville spring stack.
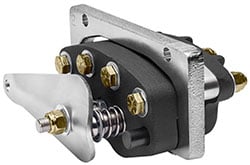
Mechanical Brakes
Mechanical brakes are simpler. They don’t require an external power source - just a lever. Mechanical brakes exert force effectively to objects in rotary or linear motion. They are a good option where air or hydraulic power is not available or desired. One example is an industrial cart with a manual braking lever.
Fix-mount Brakes v. Floating Brakes
Brakes can either be ‘fix-mounted’ or mounted to ‘float.’ Brake housings are mounted securely to the equipment when they are fix-mounted. Housings that are designed to float typically slide freely on pins or shoulder bolts until activated. The caliper releases from the braking surface when pressure is released and reverts to float. When fix-mounted, a double-live-sided brake is typically used. Both sides of the unit have pistons that force the pads to engage the braking surface. The friction pads will ‘lift’ away from the surface when not engaged. Some prefer to have the friction pads retract with springs. This video explains the difference in terms of how they are mounted.
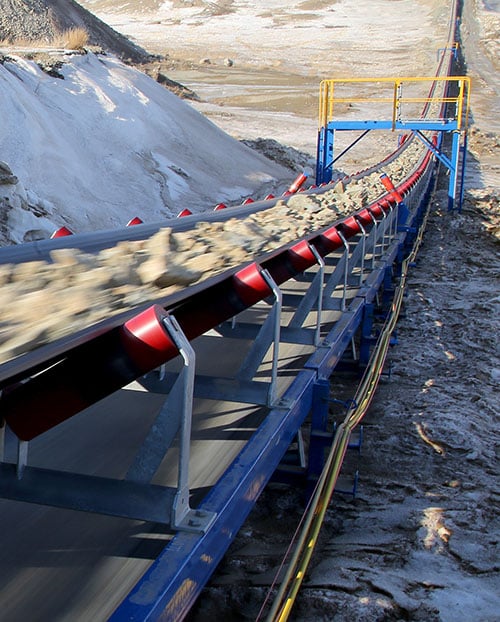
Creative Brake Caliper Solutions
Good brake manufacturers listen to customer needs and engineer new solutions on a regular basis. Often, those solutions—intended for one application—can be applied in many areas. W.C. Branham brakes are frequently used in the following ways:
- Conveyors
- Hose reels
- Indexers
- Manipulator arms
- Packaging
- Printing presses
- Web and wire tensioning
- Wind energy
- Paper and corrugated
- CNC machinery
- Winches
Braking on a Rail
Need to stop something moving in a linear path on a rail? A caliper disc brake can do that very well. As long as it is a flat surface with two parallel faces, straight or slightly curved, W.C. Branham brakes can be used.
Disc brakes used on a rail can improve safety and save space (especially where loads are suspended vertically). The use of caliper disc brakes for linear systems is expanding. Here are some common examples:
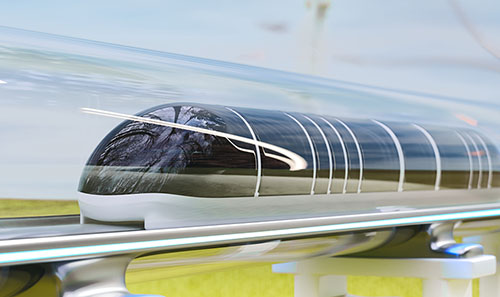
- Cart on a rail in a manufacturing process.
- Overhead gantry systems or jib cranes.
- Elevator emergency brakes.
- Linear indexing equipment, especially in medical device and pharmaceuticals manufacturing.
- Linear robotics applications like a welding machine on a rail that moves and welds in many positions.
- Renewable energy industries and ocean wave energy systems, where linear brakes hold the device in place for structural maintenance.
Futuristic transportation such as a Hyperloop pod-style car that rides on rails.
Stainless Steel Brakes
Stainless steel is an unsurpassed material in durability. It is excellent in harsh environments or where heavy industrial cleaning is important. The FDA and USDA require stainless steel in most food processing.
Both aluminum and stainless steel brakes are light, but stainless has some distinct advantages. It resists corrosion, never needs to be painted or coated, can withstand harsh acid and alkaline chemicals, and withstand high-pressure, high-heat wash downs. Consider stainless steel brakes if any of these conditions apply to your application.
Type of Brake Applications
How a brake will be used informs which kind you need. Here is background information on various applications.
Dynamic Stopping
How much torque you need for dynamic stopping is determined by the weight of the rotating mass you’re stopping, its shape, its radius of gyration, its RPMs, and the required stopping time.
To find out if a particular brake caliper has the torque you need, multiply its tangential force (which a brake manufacturer can tell you) by the braking radius of a specific disc diameter. This will tell you if that brake/disc combination can meet your torque requirements.
W.C. Branham offers caliper disc brakes that can provide anywhere from 600 to 150,000 inch pounds of braking torque. Get a copy of our product guide to explore them all.
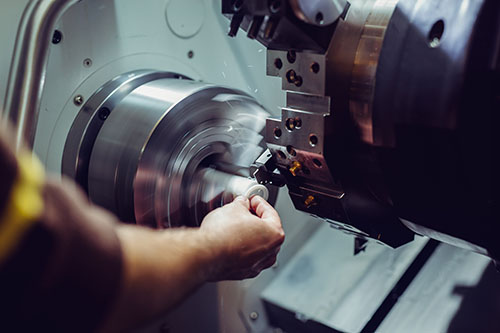
Frequent Stopping
Each stop creates friction and heat for a brake. It is crucial a brake/disc combination can adequately dissipate that heat. In calculating the torque needed to stop within a certain time you will figure out the BTUs per stop, then determine BTUs per hour, then determine the amount of exposed disc area needed to dissipate the heat.
Friction pad wear life is an important performance factor to consider for brakes that are used frequently. To calculate the life of a pad, you'll figure horsepower hours per stop, then determine the life in terms of the number of stops.
Static Holding
Calculating the brake size needed for a static hold application is relatively straightforward. First, determine the amount of torque necessary to accomplish the holding. Then select a disc brake caliper combination that can handle it.
Tensioning
When a brake is providing a constant torque to a rotating mass for tensioning, it is in continuous duty. This means there is continuous heat being created. Just like a brake used for frequent stopping, you need to consider how that friction will impact the wear life of the pads and if it can dissipate the heat appropriately. Again, you'll figure out BTUs per hour, then the heat dissipation for your tensioning application.
This video and the cheat sheets below can help you get started on determining the size brake caliper you need.
Getting the Right Size Caliper Disc Brake
Once you know the kind of brake you need, sizing it is the next step. This can be complex. Speaking with experts may be a good place for you to start. You don't have to memorize a bunch of formulas to size your caliper disc brake. Visit this page for a brake sizing calculator you can download and use anytime.
There are three big things you need to know to size a brake correctly.
- What is the required torque or braking force for the application?
- What space is available for the disc or rotor? This is important because a larger disc will produce higher torque.
- How much available pressure is there from your power source? The more pressure available (either pneumatic or hydraulic), the greater the torque you’ll be able to produce from the same sized brake. Available pressure also impacts the size/model of spring applied brakes. Knowing the available lever force is necessary in determining mechanical brake sizes.
You need good information in each of these areas in order to make a decision on the appropriate brake size.
Brake Pads and Friction Coefficients
There are three things to consider when selecting brake pad material: coefficient of friction, wear rate, and energy capacity. W.C. Branham offers brake pads with friction coefficients ranging from .21 up to .55.
Lower friction coefficients are suitable for tensioning and constant drag applications. High coefficient materials are better for static holding to maximize the braking force. Brake pads are most commonly made from materials that are either organic, semi-metallic, or sintered metal.
Organic brake pads have the lowest energy capacity limits, then semi-metallic brake pads are in the middle, and sintered metal pads have the highest energy capacity. Picking the right one is important in energy dissipation.
Note: disc temperature should not exceed 300℉, to ensure the longest service life. The amount of heat dissipated per hour at any given temperature greater than ambient air is considered to be directly proportional to the amount of exposed area on the disc. Therefore, disc thickness should be as small as possible. The standard is either 5/32" or 1/4".
Next Steps
If you still have questions after exploring this guide to selecting an industrial brake caliper, the next step is to get in touch with your brake manufacturer. At W.C. Branham, we have more than 1,300 standard products available, chances are we offer what you need! If you’re looking for something more customized, we can do that too. Our team has extensive experience and expertise designing and manufacturing custom solutions. Click here to tell us about your application needs or explore our caliper brake offerings by downloading the guide below. We look forward to working with you.