Types of Right Angle Gearboxes
While there are sub-varieties within these main categories, there are 4 main types of gearboxes:
- Worm
- Bevel
- Helical
- Planetary
Worm Gearboxes
A worm gear set actually looks a lot like it sounds—there is a worm that drives a gear. The worm, a shaft with a spiral thread, engages with and drives the gear. This design enables control over rotational direction, helps regulate speed, and adds higher torque transmission.
There are many sub-varieties of worm gears, including single-throated, non-throated, and double-throated.
-
Non-throated. Instead of a continuous thread, this style has a single moving point that contacts the gear. The minimal contact makes this type of worm drive most vulnerable to wear and tear from high unit load.
-
Single-throated. This variation can withstand high unit loads with less wear. Its concave helix wraps around the worm, making continuous contact with the gear.
-
Double-throated (called hourglass or cone). This style can withstand the highest unit loads without excessive wear and tear, because it has concave teeth on both the worm and the gear, doubling the contact area.
Worm drives can be designed with right-hand or left-hand gearing, allowing them to turn either clockwise or counterclockwise. With an internal helical gear, both parts must be the same hand. With external helical gears that function in parallel, the hands must be opposite.
Worm gears are used in low to moderate-horsepower applications. They offer low initial cost, high ratios, and high output torque in a small package. Consider using worm gears in these situations:
-
A high ratio is needed in a compact package. Worm gears can have a low number of threads, so higher ratios can be accomplished with fewer gears.
-
Quiet operation is required. The sliding action of worm gears is quieter than other gear types.
-
When back driving is not desirable. Since worm gears only work in one direction, their self-locking characteristics aid braking and avoid back driving.
Worm gears are less efficient than most other gear combinations. Their typical efficiency ranges from 50-90%, depending on gear ratio, lead angle, and friction factor. For comparison, helical gears range from 94-98% efficiency, while spiral bevel gear efficiency ranges from 95-99%.
Branham manufactures three types of right angle (worm drive) gearboxes: hollow bore single shaft, hollow bore double shaft, and hollow bore only. Each model can be spec’d in numerous bore sizes and gear ratios.
Bevel Gearboxes
Years ago, it was expensive and very difficult to make spiral bevel gearboxes. And while the precision necessary to craft such beautiful and intricate pieces is still tricky, with the right attention to design and fabrication, it's much more doable.
A bevel gearbox, as its name suggests, contains two interlocking bevel gears. On a standard gear, the pitch surface (that carries the teeth) is cylindrical. On a bevel gear, the pitch face is conical. The angle formed by the pitch face and the axis on which it’s mounted is called the pitch angle. Often, bevel gears work at right angles, but they can be designed to function at any pitch angle. A hand drill is an example of a tool that uses a 90o bevel gear.
Bevel gears are classified by their geometry, and each type of bevel gear offers its own specialty or advantage. Here is a list of bevel gear examples:
- Straight bevel gear. On a straight bevel gear, the teeth are straight–but they taper toward the apex of the cone-shaped surface. This is the most common type of bevel gear. It functions well, but the operation can be noisy, especially at high speeds or under heavy loads.
- Spiral bevel gear. On a spiral bevel gear, the teeth are curved and set in a spiral, so they contact their counterparts more gradually. This smoother operation eliminates the noise of a straight bevel gear, while reducing the risk of tooth breakage.
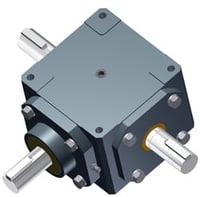
- Zerol® Bevel Gear. A zerol® bevel gear also has curved teeth, but they are not angled in a spiral, so the teeth align with the axis.
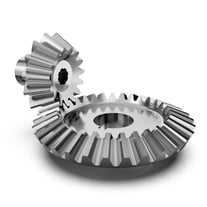
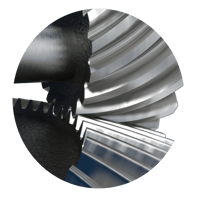
By nature, bevel gear design is highly intricate and complex. It takes meticulous planning, design, and manufacturing to achieve the desired operational result.
There are many advantages of bevel gear design:
- Bevel gears are on-plane. The input and output shafts are at a perfect right angle to each other, not offset vertically. This allows a spiral bevel gearbox to simply turn a corner to deliver the power you need where you need it.
- Bevel gears are precise. With less than half of a degree of backlash, bevel gears waste less torque or power in the slope of the gearbox. This is a feature of the intricate spiral bevel gear design, which has to be made to very exacting specifications.
- Bevel gears can easily be made into a three-way coupling. Power can be transmitted left, right, or in both directions with the same shafts. This makes it easier to split the power from one motor to operate several things at once, saving on motor cost and maintenance.
Helical Gearboxes
Helical gearboxes are known for their smooth and quiet operation, making them a reliable choice in various industrial applications. Their design features gear teeth angled along the axis of the gear and resemble a section of a helix. While helical gears provide certain advantages over other types, such as improved load capacity and quieter operation, their efficiency typically ranges around 60%, especially in right-angle configurations. They are well-suited for fractional horsepower applications, where precision and quiet operation are prioritized over raw power.
Common uses for helical gearboxes include industrial applications such as packaging, cutting, labeling, and other machinery that requires smooth and efficient gear operation.
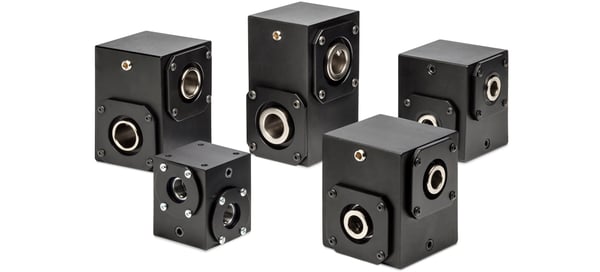
Planetary Gearboxes
An age-old design, the planetary gearbox got its name because the different gears move together like planets. A center gear turns, moving multiple gears around it, mirroring the gravitational pull of planets in our solar system.
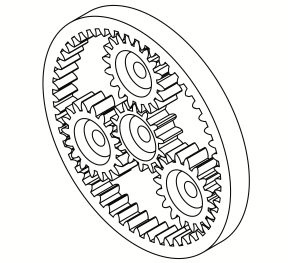
Planetary gearboxes have multiple benefits:
- They have higher torque. Because the torque is divided over 3 gears at equal dimensions, the torque is almost three times higher than typical gearboxes.
- They’re more compact, and therefore have a low mass inertia.
Keep in mind, not every solution requires a cookie-cutter gearbox—in fact, many applications have unique challenges that just can’t be satisfied by one of the basic options.
Selecting the Appropriate Gearbox for Your Application
Within the world of gearboxes, there are so many configurations that choosing the right product for your particular mechanical design can be challenging. Custom gearboxes are more common, chiefly because manufacturing to specification is easier than ever, with newer machine tools as well as design and automation software.
So, when determining the right angle gearbox that will work best for your mechanical design, it’s important to identify the key aspects of your design and application. You can review the answers to some of our commonly-asked gearbox questions or reference our Gearbox Selection Checklist for help with this.
In addition to the checklist questions, there are five important factors to consider when choosing your gearbox design.
1. Size
Some of the most common mistakes made in the engineering design process have to do with improper sizing. Our standard-size right angle gearboxes range from 2.87 to 6.6 inches tall. A more compact option is the MICROGEAR series (the smallest of which is under 1.5 cubic inches). We know that it's best to find an exact fit, which is why we specialize in custom design products, too.
Check out this video on right angle gearbox sizing from our very own VP of Engineering and General Manager, Chad Randleman.
As Chad stated, the three areas you need to consider when sizing a right angle gearbox are:
- Required torque for the application. Along with the required output torque, you’ll need to know the required RPM and shaft rotation for your application.
- Radial or axial loading of the application. If you have radial or axial loading applied to your gearbox shaft, you’ll want to support the shafting externally using bearing blocks.
- Duty cycle of the application. For light to moderate duty applications, gearboxes would be considered lubricated and lubed for life. For more severe duty applications, put them on a regular maintenance schedule for relubrication.
Beyond these areas, you should also assess your horsepower and input speed requirements, target output speed or torque, and load support needs. High-speed right angle gearboxes are particularly essential for high-speed, high-torque applications, where reliability is key. These gearboxes are commonly used in packaging, bottling lines, food processing, and heavy manufacturing industries such as cement, steel, and mining. Additionally, high-speed roll-up doors in locations like car washes, food and beverage operations, and medical facilities also benefit from these gearboxes.
When choosing a gearbox, consider how it will impact your operational efficiency, reliability, performance, and long-term costs. Key details include:
- Required output and input speed
- Desired gear ratio (1:1, 2:1, 3:2, etc.)
- Duty cycle frequency, including required starts and stops
- Environmental factors like washdown, chemicals, or extreme temperatures
For some types of applications, you’ll also want to specify the acceptable amount of backlash (space between two meshing gears). This assures optimal lubrication, so the gears won’t lock up.
Learn more about high-speed right angle gearboxes.
2. Desired Rotation
If your application demands a right angle gearbox, check if the design calls for a left-hand or right-hand rotation.
The main differentiation between the right-hand and left-hand versions of right angle gearboxes is the rotation of the gear drives.
For example, if the A-Bore is rotated clockwise, the B-Bore would rotate clockwise with a right-hand configured gearbox and counter-clockwise with a left-hand configured gearbox.
With many standard types and sizes available, and the ability for specialty shaft configurations, it’s vital to choose the right angle gearbox for your application. Having multiple mounting options also helps simplify your design considerations.
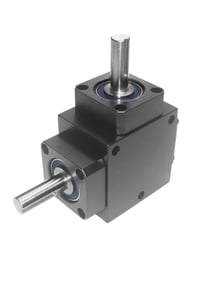
3. Mounting Requirements
Mounting your gearbox correctly is essential to its performance, durability, and ease of maintenance. That's why considering mounting requirements when selecting a gearbox is so important. Proper alignment and secure mounting help the gearbox run efficiently and prevent unnecessary stress on internal components, reducing the risk of premature wear and failure.
There are several key considerations for mounting a gearbox:
- Orientation: Determine whether the gearbox will be mounted vertically or horizontally, as this can affect lubrication and load distribution. Horizontal mounting is more common, but vertical mounting may be necessary in applications with space constraints.
- Mounting Points: Ensure that the gearbox has sufficient and properly spaced mounting points to handle the loads and vibrations of your application. This will help prevent misalignment and maintain the integrity of the system over time.
- Clearance: Make sure there is adequate clearance around the gearbox for maintenance and inspections. Restricted access can complicate regular upkeep, increasing the risk of breakdowns and downtime.
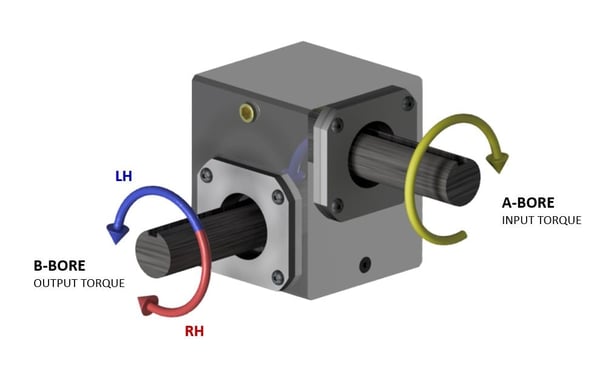
4. Environmental Conditions
Will your gearbox have to withstand shock, vibration, or wet washdown conditions? You may need corrosion-resistant materials or plating, or you may want to spec stainless steel shafts and housing.
Stainless steel gearboxes are used in various environmentally-impacted industries, such as
- Food processing
- Beverage bottling
- Meat packing
- Pharmaceutical or medical device manufacturing
- Chemical processing
- Packaging equipment
- Marine industries
- Any wash-down application
Some of these operations require that gearboxes be lubricated with H1 or H2 food-grade grease. With stainless steel gearboxes, that doesn’t limit your design options.
Speaking of lubrication, the five common right angle gear drive lubrication options to remember for proper installation and maintenance depending on your particular operating conditions are:
- Gearing Type
- Loading
- Gear Speed
- Materials Compatibility
- Ambient Temperature
Keep in mind, there’s also always the option of building a custom gearbox for stainless systems.
5. Customization
Custom and standard gearing aren’t mutually exclusive. Our standard-size right angle gearboxes range from 2.87 to 6.6 inches tall, and we also offer more compact options, like the MICROGEAR series, which is under 1.5 cubic inches. When fully custom gearboxes aren’t a feasible option (for example, quantities aren’t high enough), choose a manufacturer with built-to-order gearboxes from standard modular subcomponents. Look for manufacturers that employ the latest CAD software, CAM software, and machine tools to streamline post-processing work and reduce one-off costs.
After you’ve chosen a gearbox, discuss your application with the manufacturer or their technical representative. Once installed, perform several test runs to replicate typical operating scenarios. If unusually high heat, noise, or stress is present, repeat the gear-selection process–or contact your representative for assistance.
After you’ve chosen a gearbox, it is advised to discuss your application with the manufacturer or their technical representative. Once installed, perform several test runs to replicate typical operating scenarios. If unusually high heat, noise, or stress is present, repeat the gear-selection process or contact your representative for assistance. You'll find that they are willing to assist you in making a successful installation for your application.
Selecting the Appropriate Gearbox Supplier
If you’re in the market for a right angle gearbox, you’ll need to find a high quality gearbox supplier. But how can you determine whether someone is the “right” gearbox supplier?
First, confirm whether they manufacture your preferred type of right angle gearbox. Then, take note of their product selection. Do they offer multiple types of gearboxes? If so, they’re likely more flexible in their capabilities.
To make this a bit easier, refer to our Gearbox Selection Checklist. If the supplier can check these boxes, they’re worth exploring further.
Also see if they offer any custom gearbox solutions. Even if the application you’re working on today doesn’t need it, you may need a custom gearbox later.
Pro tip: When visiting their website, try to see who they’ve worked with in the past and what they’ve accomplished. If the work they’ve done in the past lines up with the requirements of your application, they might be the right gearbox supplier for you. Be sure to also check their reviews online, if they have any!
It’s also important to see if they offer any custom gearbox solutions. Even if the application you’re working on today doesn’t need it, you may need a custom gearbox down the line!
Pro tip: When visiting their website, try to see who they’ve worked with in the past and what they’ve accomplished. If the work they’ve done in the past lines up with the requirements of your application, they might be the right gearbox supplier for you. Be sure to also check their reviews online, if they have any!
How to Extend the Life of Your Gearboxes
.jpg?width=300&name=4304-0600%203SB2.57SBM.625%20TRANSPARENT%20IMAGE-2%20(1).jpg)
Automation and the laws of physics dictate that all moving parts wear out over time, including your right angle gearbox. Industrial settings are demanding and unforgiving. High speeds, high temperatures, wash down requirements, and other factors take their toll.
Right angle gearboxes require less maintenance than many other industrial components, but they still need upkeep. Developing problems can damage seals, bearings, bolts, and other internal components–or even cause the entire gearbox to fail.
You can prevent untimely problems and extend right angle gearbox service life with a few simple precautions, including preventative maintenance, adequate product selection, and custom product application when necessary.
When to Repair vs. Replace Gearboxes
Wear and tear is unavoidable for industrial machinery, operating in settings with high temperatures, high speeds, outdoor dirt, or harsh washdowns. Nothing lasts forever, and even the highest quality components eventually break down.
Right angle gearboxes, in general, are low-maintenance. But if something goes wrong, how can you tell if the gearbox needs repair or replacement?
The sooner you detect emerging problems, the better your chances of avoiding major repair or replacement costs. Developing problems can also push gearbox components out of spec, which weakens performance and speeds further damage.
Here are some signs to look for and steps you can take to troubleshoot gearbox problems.
- Overheating
- Leaks
- Misalignment
- Noise
- Unexpected loads
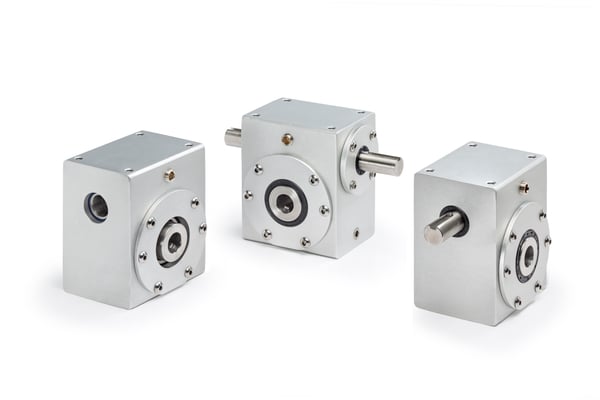
Preventative maintenance is the most affordable approach to gearbox longevity. The time you spend on maintenance now can keep operations running smoothly–and save you both time and money later. Here are some tips to help keep your gearboxes running smoothly:
- Schedule regular inspections. They can uncover problems that lead to damaged seals as well as internal bearings, bolts, and so on. Look for grease leakage and any signs of wear on gears.
- Check for signs of heat buildup.
- Regularly clean the gearbox to help prevent possible contamination. Never use solvents to clean the exterior or any internal parts. Make sure the gearbox is properly lubricated.
In the end, it all boils down to understanding the requirements of your unique application, paired with an understanding of your right angle gearbox options. If you need any help, contact the Branham team. We’ve been helping customers find solutions to their unique challenges for 40 years and look forward to the opportunity to serve you.
Back to top